BLUE CHIP CUSTOMER REFERENCES
Leachate Treatment for Waste Incineration Plant
Pre-treatment + Anaerobic UASB + MBR + Tubular Ultrafiltration + DTRO/STRO High Pressure Reverse Osmosis
The anaerobic UASB process removes 75% to 90% of COD from leachate.
The MBR consists of:
- A denitrification tank
- A nitrification tank
- An external ultrafiltration system
The MBR targets ammonium nitrogen and remaining COD.
The biologically pre-treated leachate is directed into the DTRO/STRO reverse osmosis system.
The DTRO/STRO system operates at high pressure, achieving a recovery rate of 80% to 85%.
The produced water consistently meets discharge standards.
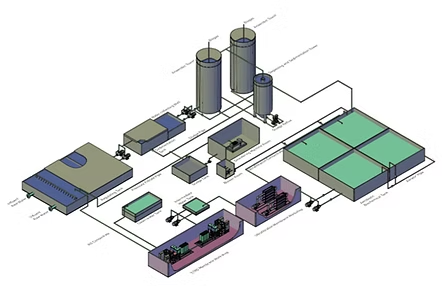
Leachate Treatment for Landfill Sites
Pre-treatment + Hydrolysis Tank + MBR + Tubular Ultrafiltration + STRO (DTRO) High Pressure Reverse Osmosis
The hydrolysis process primarily enhances the biodegradability of leachate.
The external MBR system includes:
- A denitrification tank
- A nitrification tank
- An external ultrafiltration system
The MBR system removes ammonium nitrogen with a removal rate of 99% and addresses remaining COD in leachate.
The biologically pre-treated effluent is fed into the reverse osmosis system.
The high-pressure DTRO/STRO membrane system achieves a recovery rate of 80-85%.The produced water consistently meets discharge standards.
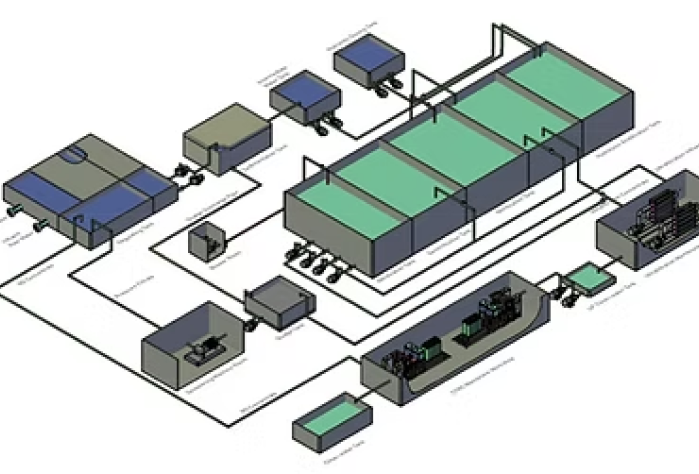
Process of CTX Wastewater Treatment
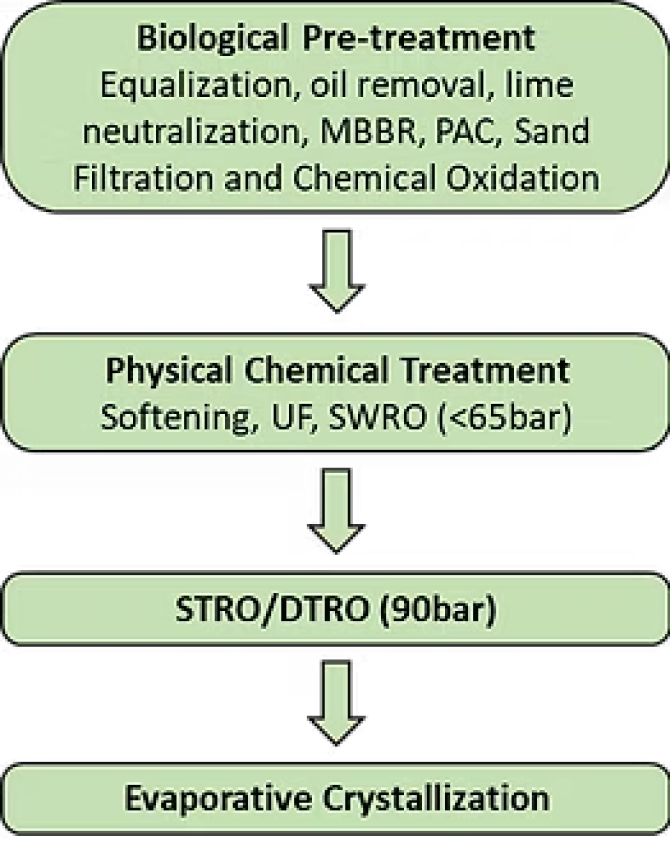
Technological Advancements:
- Economic viability of converting coal into liquid fuels (gasoline, diesel, petrochemical products)
Water Usage in Coal Chemical Industry:
- Significant water consumption for cooling systems and liquefaction gasification processes
- Results in wastewater with complex compositions
Common Contaminants in CTX Wastewater:
- Salts
- Minerals
- Sulphides
- Ammonia
- Oils and fats
- Cyanides
Coal Mine ZLD Project
Ultrafiltration, Primary Reverse Osmosis, Softening, Secondary RO, High-pressure DTRO, Evaporation/Crystallization.
- Project: Coal Mine ZLD (Zero Liquid Discharge) industrial mining wastewater treatment plant
- Capacity: 20,000 m³/day
Treatment Process:
- Ultrafiltration (UF)
- Primary Reverse Osmosis (RO) filtration
- Softening process
- Secondary RO filtration
- High-pressure DTRO technology
- Evaporation/crystallization
Membrane Concentration Stage:
- Salt content increased from 5,000 mg/L to 136,000 mg/L
- Concentration factor: 30
- Water Recovery Rate: 97%
- Reclaimed Water Quality: Meets reuse standards for power plant operations
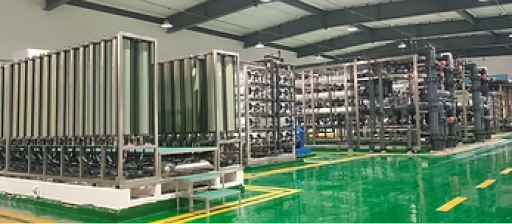
Process of STRO/DTRO for
Wet FGD (flue-gas Desulfurization) Wastewater Treatment
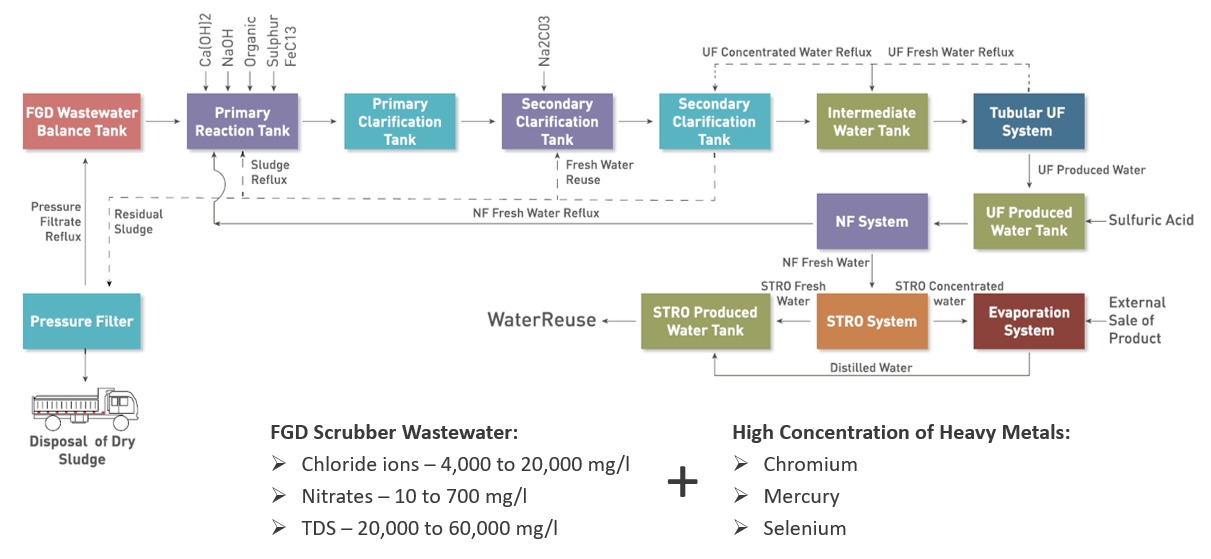
Process Water Treatment Plant for beverage
Ultrafiltration + Activated Carbon Filter + UV disinfection + Reverse Osmosis
- Upgrade existing Process water treatment plants in beverage production sites.
- Provided design, equipment procurement, assembly, installation and commissioning services
- Delivered solutions with 13 trains of 75m3/h treatment capacity for process water
- Adhere to EHEDG specification
- More than 96% increase in water efficiency, re-using process water as cooling and boiler water and reducing product water by 15%
- Additional reduction of operating cost and energy consumption
- Efficient delivery of a full turn-key solutions in 20 weeks
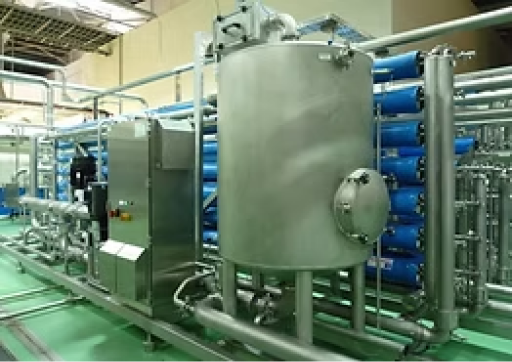
Leachate treatment of domestic landfill in Spain
- Processing scale: 2000 m³/ day
- Treatment process: secondary STRO+ resin adsorption
- Influent mass: conductance >50000µS/cm; COD>10000mg/L, ammonia nitrogen >5000mg/L, alkalinity >9800mg/L
- Production water quality: COD<20mg/L, ammonia nitrogen <5mg/L
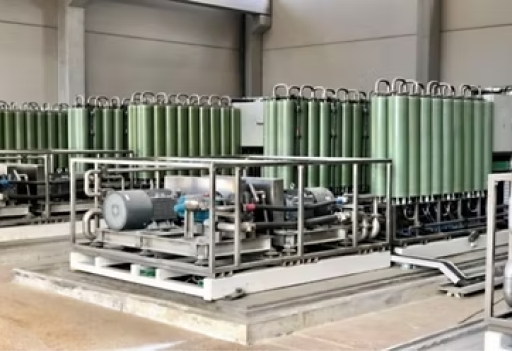
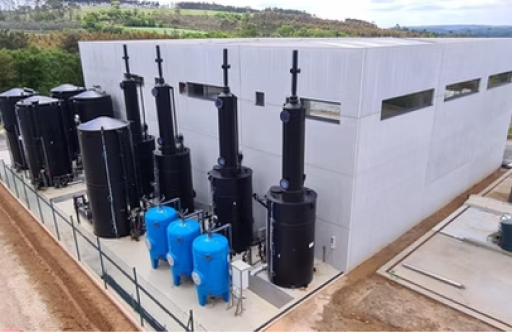
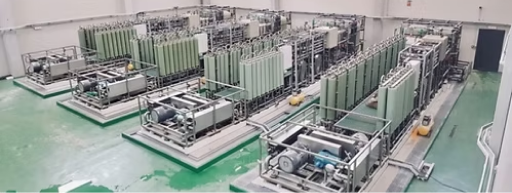
Iron and Steel making Plant’s South Blast Furnace Gas Desalting and
Washing Tower Concentrate
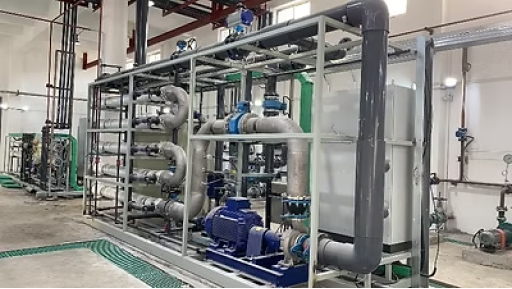
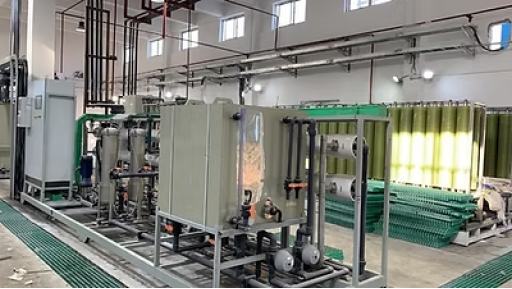
Iron and Steel making Plant’s South Blast Furnace Gas Desalting and Washing Tower Concentrate
- Treatment Scale: 250 m³/day
- Treatment Process:
- Tubular ultrafiltration membrane
- Primary DTRO membrane
- Secondary roll RO membrane
- Problem Addressed:
- High COD (Chemical Oxygen Demand)
- High ammonia nitrogen
- High total salt content
- Solution: Wastewater resource recycling of concentrated water from the blast furnace gas desalting washing tower in the steel industry